Introduction
Bucket wheels are critical components in large-scale mining and material handling equipment, directly influencing the performance, energy efficiency, and longevity of machines such as bucket wheel excavators and reclaimer systems. Optimizing these components for weight reduction not only improves machine balance and energy consumption but also enhances durability and material handling efficiency. This article explores the various types of bucket wheels and their configurations, analyzing their design principles, performance characteristics, and technical considerations through the lens of advanced Finite Element Method (FEM) simulations.
The Challenge of Weight Optimization
Bucket wheels are positioned at the tip of long booms, which amplifies their impact on a machine’s dynamics. Their mass significantly affects counterweight systems, structural stability, and energy requirements. Optimizing bucket wheel weight offers several interconnected benefits:
- Enhanced Dynamics: Lower stress on bearings and booms improves machine stability and lifespan.
- Energy Efficiency: Reduced weight minimizes power requirements, particularly during operation and material transport.
- Cost Savings: Lightweight designs use less material, reducing both manufacturing and maintenance costs of the entire machine.
MCI has embraced these principles, applying state-of-the-art design approaches and materials to advance bucket wheel efficiency while maintaining structural integrity.
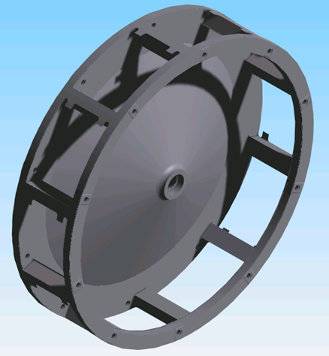
Cell-Less Type Bucket Wheel
The cell less type bucket wheel, has become the modern standard in bucket wheel design. It eliminates compartments entirely, relying on an open structure paired with a ringshaped chute (“ring chute”) to prevent premature material discharge. This streamlined configuration reduces weight, enhances cutting efficiency, and facilitates smoother material flow. Its ability to handle cohesive, wet, or mixed materials makes it ideal for today’s diverse mining requirements.
FEM analyses confirm that cell-less wheels maintain structural integrity under high cutting speeds and variable loads, delivering superior performance across a range of operational conditions.
Configurations of Bucket Wheels
Double-Walled Design: Proven Reliability with Trade-offs
The double-walled configuration remains a benchmark for heavy-duty applications. It consists of two parallel circular plates connected by a network of stiffeners and transverse beams, ensuring uniform stress distribution and minimal deformation under extreme loads. This design excels in handling dense, abrasive materials like coal and iron ore.
A significant variation is the double-walled conical design, where the plates taper outward to improve material flow and reduce clogging risks. FEM analysis demonstrates that these designs retain stability even under asymmetric loading conditions, offering unmatched reliability for high-capacity operations.
However, the double-walled configuration’s durability comes at the cost of increased weight, which can strain counterweight systems and increase energy consumption.
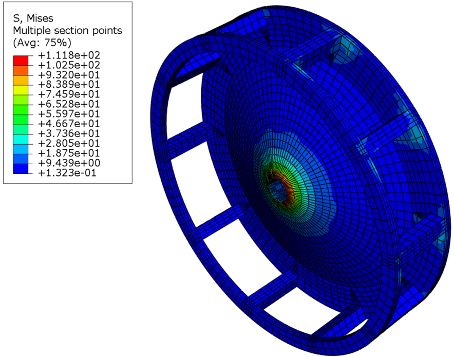
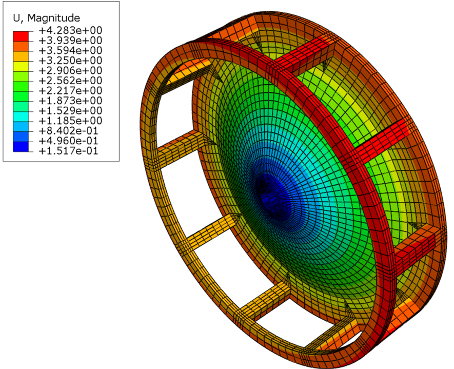
Single-Plate Design: Lightweight with Limitations
The single-plate configuration prioritizes weight reduction by using a single conical plate as the primary structural component. This design simplifies manufacturing and reduces material costs while improving material flow efficiency. Its conical geometry manages axial and tangential forces effectively, making it well-suited for sticky or clay-rich materials.
However, single-plate designs are prone to deformation, particularly at shaft connections. FEM simulations reveal deformation values reaching 27.34 mm under peak loads, necessitating careful reinforcement at critical points to maintain performance under heavy-duty conditions.
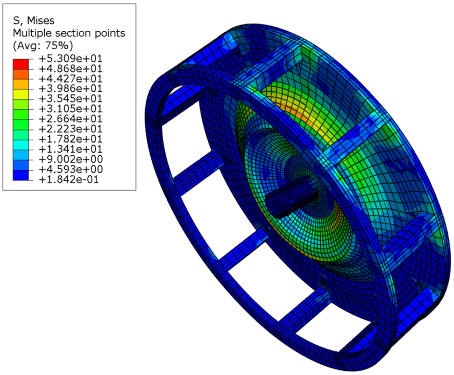
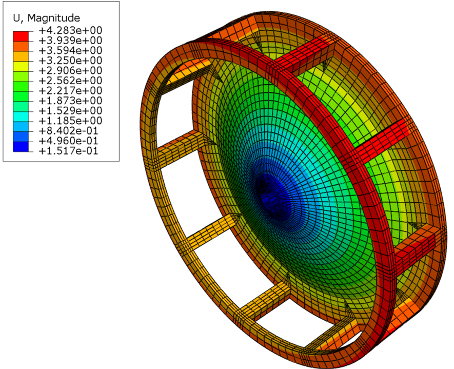
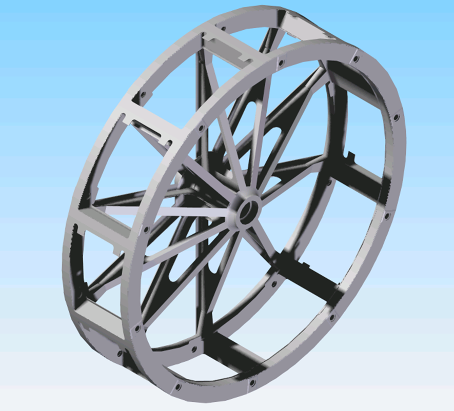
Spoke Wheel Design: Modern Innovation with Potential
The spoke wheel design achieves substantial weight reductions by replacing solid plates with strategically arranged radial spokes. Each spoke acts as a load-bearing element, transferring forces efficiently between the hub and outer ring. This configuration minimizes material usage while maintaining structural integrity for medium-duty applications.
Optimizing spoke geometry is essential to address stress concentrations at junctions. FEM analyses recommend the use of curved transitions and variable thicknesses to reduce peak stresses. While highly efficient in terms of weight, spoke designs require meticulous maintenance due to their susceptibility to wear and material buildup.
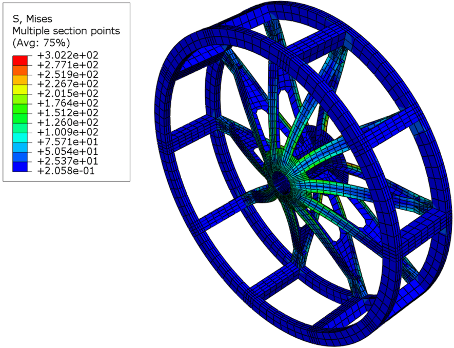
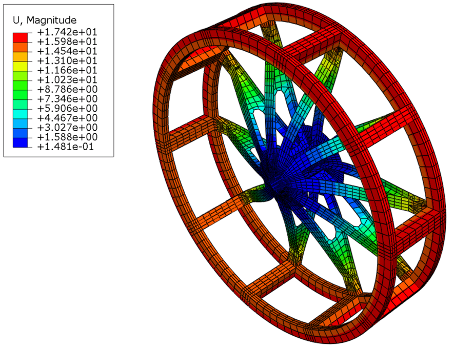
Technical Insights from FEM Analysis
Finite Element Method (FEM) simulations are essential for validating bucket wheel designs under realistic operational conditions, highlighting differences in their response to dynamic loads, stress distributions, and deformation challenges.
Double-walled wheels offer superior rigidity through dual-plate construction with internal stiffeners and transverse beams, ensuring even stress distribution and minimal deformation under high-capacity operations with dense materials like coal and iron ore. Despite their robustness and ability to withstand asymmetric loads, their increased weight can strain ancillary systems like booms and counterweights.
Single-plate wheels focus on weight reduction and simplicity, replacing a secondary plate with a conical single plate for material savings and better force management. FEM analyses show suitability for sticky materials but reveal vulnerabilities at shaft connections, with deformation up to 27.34 mm under peak loads, requiring reinforcements to prevent failures.
Spoke wheels optimize weight with radial spokes as load-bearing elements, achieving over 30% weight reduction compared to double-walled designs. However, their open structure is prone to wear and material buildup, emphasizing the need for maintenance. FEM studies highlight spoke geometry’s critical role in stress management.
FEM simulations provide crucial insights into optimizing bucket wheel designs, balancing performance, durability, and cost efficiency to meet the mining industry’s evolving demands.
Insights from Georg Leitner , Head of Engineering at MCI
“At MCI, our mission is to deliver innovative and robust designs, enabling our customers to achieve maximum machine performance with minimal maintenance costs. Through advanced simulation tools and efficient engineering, we create durable solutions that meet today’s challenges and stand the test of time.“ says Georg Leitner, Head of Engineering at MCI.
Conclusion
This comprehensive exploration of bucket wheel types and configurations highlights how advanced engineering and material science are driving mining innovation. By integrating cutting-edge FEM analysis and lightweight designs, MCI continues to set new benchmarks for performance, reliability, and sustainability.
Operation: Advantages of Modern Bucket Wheel Designs
In practical operations, spoke-wheel and single-plate designs in mining and material handling equipment offer clear advantages over double-walled configurations, particularly in terms of maintenance and inspection. Their open structures prevent hidden material buildup, facilitating easier cleaning and quicker inspections. This reduces downtime and operational costs.
The spoke wheel excels with significant weight reduction, minimizing stress on supporting components while maintaining structural integrity through FEM-optimized geometry. The single-plate design, ideal for sticky materials like clay, balances manufacturing simplicity with efficient material flow but requires reinforcement at critical points to counter deformation under peak loads.
These features make both designs highly efficient and cost-effective, tailored to specific operational demands.